In the production process of spunbonded nonwovens, various factors may affect the physical properties of the products.
The analysis of main factors affecting fabric properties is helpful to control the process conditions correctly and obtain nice PP spunbonded nonwovens with good quality to fit customers’ applicability.
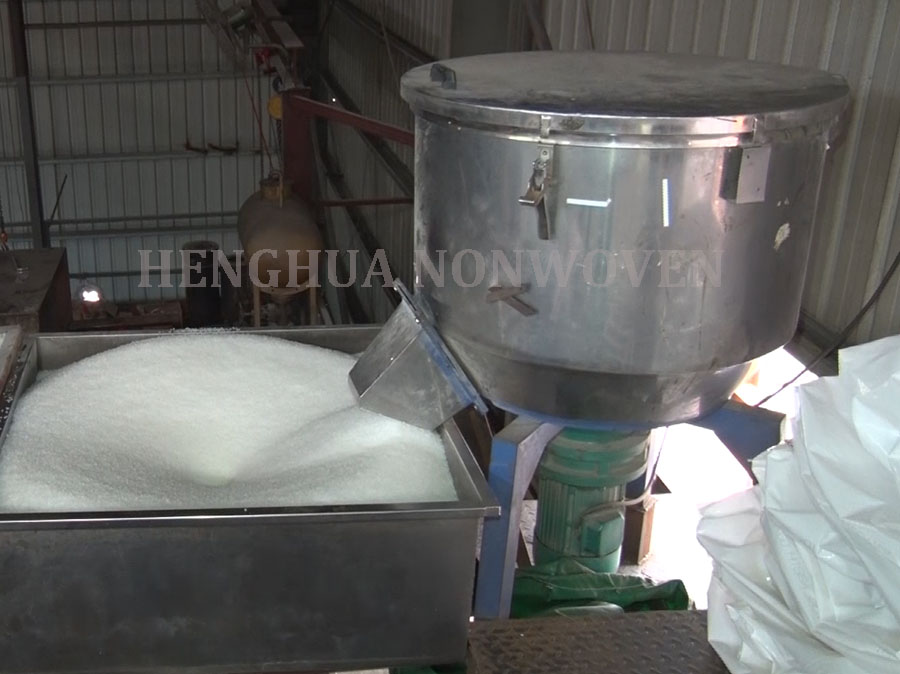
1.Polypropylene type: melt index and molecular weight
The main quality indexes of polypropylene material are molecular weight, molecular weight distribution, isotacticity, melt index and ash content.
Polypropylene suppliers are in the upstream of the plastics chain, providing polypropylene raw materials on various grades and specifications.
To make spunbond nonwoven, polypropylene molecular weight usually at range 100,000-250,000. However, it has been proved that the melt property act best when the molecular weight is about 120000. The maximum spinning speed is also high at this level.
Melt index is a parameter reflecting the rheological properties of melt. The melt index of PP particle for spunbond is usually between 10 and 50.
The smaller melt index is, the worse the fluidity is, the smaller the drafting ratio is, and the larger the fiber size which under the condition of the same melt output from the spinneret, so nonwovens shows more hard hand feelings.
When melt index larger, the viscosity of the melt decreases, the rheological property comes better, and the drafting resistance decreases. Under the same operate condition, the drafting multiple increases. With the increase of orientation degree of macromolecules, the breaking strength of nonwoven will be improved, and the yarn size will be decreased, and fabric will feel more soft.With the same process, the higher the melt index, the fracture strength perform more well.
2. Spinning temperature
The setting of spinning temperature depends on the melt index of raw materials and the requirements of physical properties of products. The higher the melt index require higher spinning temperature, and vice versa. The spinning temperature is directly related to the melt viscosity. Due to the high viscosity of melt, it is difficult to spin, resulting in broken, stiff or coarse yarn mass, which affects the quality of products.
Therefore, in order to reduce the viscosity of the melt and improve the rheological properties of melt, increasing the temperature is generally adopted. The spinning temperature has a great influence on the structure and properties of fibers.
When the spinning temperature set higher, the breaking strength is higher, the breaking elongation is smaller, and fabric feels more soft.
In practice, the spinning temperature usually set 220-230 ℃.
3. Cooling rate
In the forming process of spunbonded nonwovens, the cooling rate of yarn has a great influence on physical properties of spunbonded nonwovens.
If fiber cooled slowly, it obtain stable monoclinic crystal structure, which is not conducive for fibers to draw.Therefore, in the molding process, the method of increasing the cooling air volume and reducing the temperature of the spinning chamber is usually used to improve the breaking strength and reduce the elongation of the spunbonded non-woven fabric. In addition, the cooling distance of the yarn is also closely related to its properties. In the production of spunbonded non-woven fabrics, the cooling distance is generally between 50 cm and 60 cm.
4. Drafting Conditions
The orientation degree of molecular chain in filament is an important factor affecting the breaking elongation of monofilament.
The uniformity and breaking strength of spunbonded nonwovens can be improved by increasing the suction air volume. However, if the suction air volume is too large, it is easy to break the yarn, and the draft is too severe, the orientation of the polymer tends to be complete, and the crystallinity of the polymer is too high, which will reduce the impact strength and elongation at break, and increase the brittleness, resulting in the decrease of the strength and elongation of the non-woven fabric. It can be seen that the strength and elongation of spunbonded nonwovens increase and decrease regularly with the increase of suction air volume. In actual production, the process must be adjusted according to the needs and actual situation in order to obtain high-quality products.
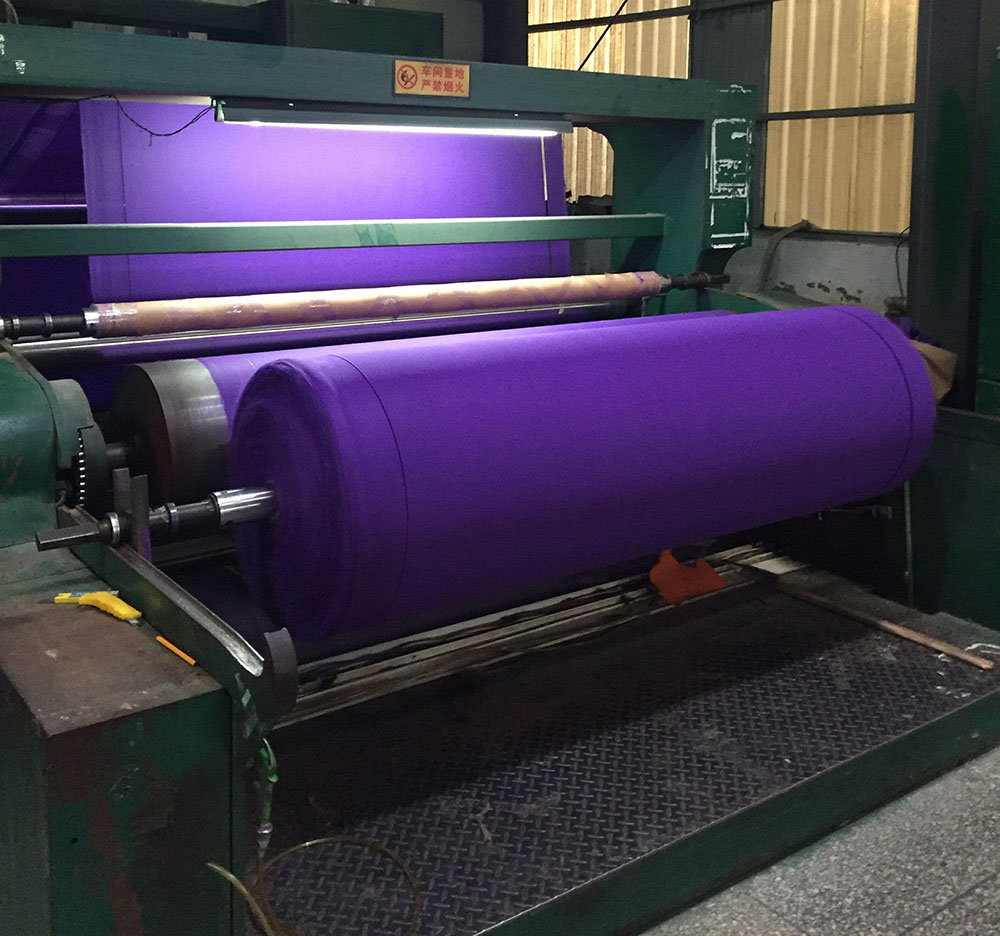
5. Hot rolling temperature
After web formed by drawing,it is loose and must be bonded by hot rolling. The key is to control the temperature and pressure. The function of heating is to soften and melt the fiber. The proportion of softened and fused fibers determine physical properties of PP spunbond nonwoven fabric.
When the temperature starts very low, only a small part fibers with low molecular weight soften and melt, few fibers are bonded together under pressure.The fibers in the web are easy to slip, the breaking strength of the non-woven fabric is small and the elongation is large, and the fabric feels soft but possible to become fuzz;
When the hot rolling temperature increases, the amount of softened and melted fiber increases, the fiber web is bonded closely, not easy to slip. The breaking strength of the non-woven fabric increases, and the elongation is still large. Moreover, due to the strong affinity between the fibers, the elongation increases slightly;
When the temperature rises greatly, the strength of nonwovens begins to decrease, the elongation also decreases greatly, you feels fabric become hard and brittle, and the tear strength reduce.For low thickness items, there are less fibers at the hot rolling point and less heat required for softening and melting, so hot rolling temperature should set lower. Correspondingly, for thick items, the hot rolling temperature is higher.
6. Hot rolling pressure
In the bonding process of hot rolling, the function of hot rolling mill line pressure is to make the softened and melted fibers bond together closely, increase the cohesion between the fibers, and make the fibers not easy to slip.
When the hot-rolled line pressure is relatively low, the fiber density at the pressing point is poor, the fiber bonding fastness is not high, and the cohesion between fibers is poor. At this time, the hand feel of spunbonded non-woven fabric is relatively soft, the elongation at break is relatively large, but the breaking strength is relatively low;
on the contrary, when the line pressure is relatively high, the hand feel of spunbonded non-woven fabric is relatively hard, and the elongation at break is relatively low But the breaking strength is higher. The setting of hot rolling pressure has a lot to do with the weight and thickness of non-woven fabrics. In order to produce the products that meet the performance requirements, it is necessary to select the appropriate hot rolling pressure according to the needs.
In a word, the physical properties of non-woven fabrics are the result of the interaction of many factors.Even same fabric thickness, different fabric usage may require different tech process.That’s why customer offen been asked fabric usage.It’ll help supplier arrange production with specfic purpose and provide dear customer the most satisfied nonwoven fabric.
As 17 years manufacturer, Fuzhou Heng Hua New Material Co.,Ltd. are confident provide fabric according to customers’ demand. We have been exporting to various countries and regions and have been highly praised by users.
Welcome consult us and start the long-term cooperation with Henghua Nonwoven!
Post time: Apr-16-2021